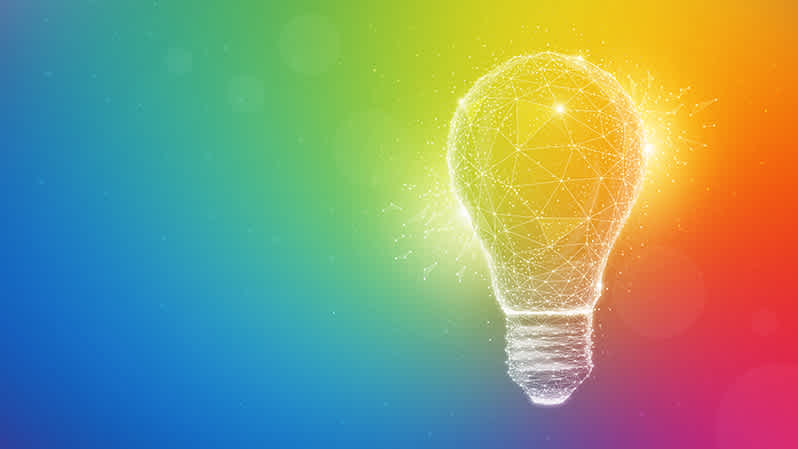
Savior Behaviors
National Safety Month: Savior Behaviors
Why Safety Observations Matter
Last week, we talked about the importance of facility audits and inspections. The human element, or the way employees perform their job duties, directly contributes to many workplace incidents and injuries. As a supplement to audits and inspections, safety observations can be a highly effective tool to modify behaviors and are a foundational component of a behavioral safety program. Observing employees as they work affords opportunities for coaching, re-enforcement of positive behaviors and increased success of eliminating unsafe behaviors before they result in an injury.
Safety observations can help:
Enrich the safety culture of your operation as well as the skill sets of managers/supervisors.
Enhance accountability across all levels.
Increase employee engagement and reduce complacency.
Reinforce positive practices and eliminate unsafe behaviors.
Allow employees to provide safety suggestions/feedback.
Provide for re-evaluation of safe work practices through live observation.
Improve job instruction/training.
Improve efficiencies that support cost reductions.
To conduct a successful safety observation, here are 5 easy steps you can take:
Announce: Approach the employee and inform them that you are doing a safety observation, highlighting that it is for safety coaching purposes.
Watch/observe: Select an employee to observe over the course of days or a week for several 2-4 minute increments of time. Notate briefly the task being performed, with attention to positive behaviors and unsafe behaviors.
Ask open-ended questions: This will help you better understand employees thought process/approach to the task being performed.
Reinforce: Proceed to reinforce positive behavior observed through use of specific examples (i.e., PPE, use of proper body mechanics, etc.); review safe work steps for the unsafe behavior observed, and emphasize the hazard(s).
Thanks and safety suggestions: Thank the employee for committing to working safely and notate a timeframe to follow up on any issues. Be sure to also secure any safety suggestions from the employee during this time.
Managers and supervisors should conduct safety observations once or twice a month, providing direct and immediate accolades for positive safe behaviors. Need help identifying what tasks to observe? Consider the following:
General Industry: Increase observations of tasks associated with Lock-Out/Tag-Out and interaction of employees with machinery/equipment.
Healthcare: Resident transfer from sit to stand or chair to bed; safe use of utensils in dietary; ladder activity with maintenance.
Transportation: Cab entry/exit (3 points of contact); load handling; body mechanics while dollying trailers.
Food/Grocers: Proper use of PPE; lifting techniques; interaction with machinery/equipment.