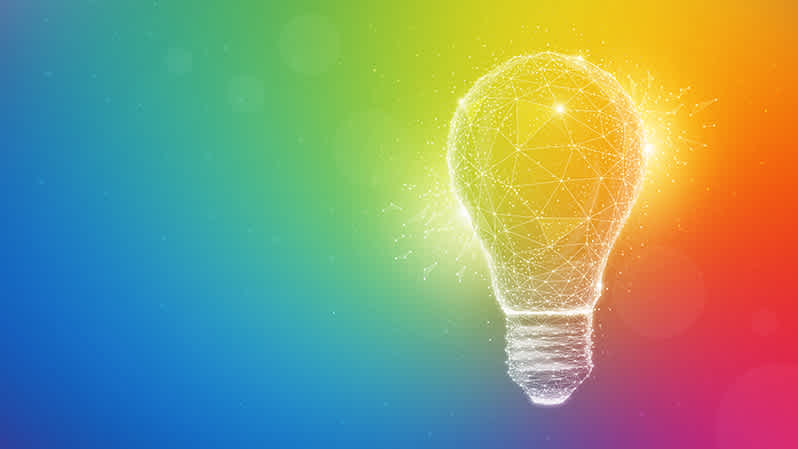
Inspect to Protect
National Safety Month: Inspect to Protect
Top 10 Safety Audit Considerations
Safety audits provide an opportunity to take a step back in your facility to look inward to see what type of condition your facility is in at a point in time. Effective safety audits can be a critical aspect of your accountability program, which can help you continually grow your safety culture. However, if an audit is done too quickly, used as a pencil whipping exercise, or not done at all, you can miss an opportunity to take your program to the next level.
The following are the top 10 things to consider when completing a safety audit within your operations.
Customize the audit to fit the need(s) of the specific department, location, facility, etc. Focus on the physical exposures within your facility.
Keep the audit concise and easy to complete.
Supervisors should take the lead on these audits. However, consider seeking staff input to the audit and include different members of the team to provide a 360 viewpoint.
Hold staff accountable for completing quality audits on a regular basis. We recommend supervisors complete audits weekly, at a minimum.
Develop a method to track and complete insufficient findings. Share the corrective action changes with the department employees as a result of the audit(s).
Celebrate the positive aspects of the audit. Simple things such as thanking the department or positively recognizing employees that keep their area in good condition goes a long way.
If your location has severity potentials that could add up to fatally injure an employee, be sure that these are reviewed with extra emphasis.
Do not overlook what you think might be basic information. If it is important, even though obvious, be sure to include this in your checklist.
Review the audits for trends and areas for improvement.
Adjust the audit regularly to keep a fresh perspective.
Each industry will have its own key areas of focus. Consider the following audits and inspections in these industries:
General Industry: Review the pillars of Loss Prevention – Lock-Out/Tag-Out, forklift safety, work from heights, and machine safeguarding
Healthcare: Resident transfers, use of gait belts, appropriate footwear, and slip-trip-fall hazards
Food/Grocers: Slip-trip-fall hazards, proper use of PPE (including footwear and hand protection), machine safeguarding hazards, and proper lifting techniques